industry portal
Green IT Panel is your premier industry portal for cutting-edge trends in manufacturing, energy, and sustainable production. We deliver actionable insights on digital manufacturing, solar integration, quality management, and factory optimization. Whether you’re streamlining operations or adopting green tech, our data-driven guides, case studies, and expert analyses empower professionals to lead in a competitive market. Stay ahead with the tools and knowledge shaping Industry 4.0
Future-Proof Your Business
Why Green IT Panel is the Ultimate Industry Portal
From digital manufacturing (think IoT-enabled assembly lines) to energy innovations (like green hydrogen integration), Green IT Panel covers the full spectrum of industrial evolution. Dive into factory operations strategies that slash downtime via predictive maintenance, or explore production techniques leveraging robotics for 24/7 efficiency.
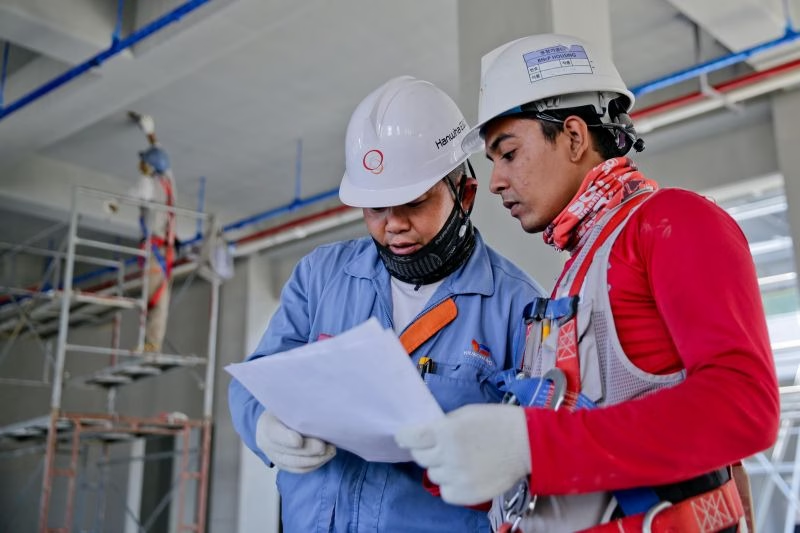
Our deep dives into quality management reveal how AI audits ensure ISO compliance, while solar analyses decode ROI for renewable transitions.
For leaders prioritizing agility and sustainability, this portal is your roadmap to tomorrow’s industry.
Latest Updates on Green IT Panel
Production Efficiency Calculation: A Comprehensive Guide
Job Shop Manufacturing: A Comprehensive Guide to Understanding Its Benefits
How to Clean Solar Panels on Roof Automatically: A Complete Guide
Lean Manufacturing System: Principles and Benefits Explained
Manufacturing Supply Chain: Key Concepts and Best Practices
Manufacturing Process Optimization: Key Strategies for Efficiency
Metal Stamping: A Comprehensive Guide to Techniques and Applications
Manufacturing Job Titles: A Comprehensive Guide to Roles in the Industry
Production Line Balancing: Techniques and Benefits for Efficiency
Industry Evolution Unlocked
Key Metrics Shaping Modern Manufacturing
AI Integration
Over 72% of U.S. factories now use AI for predictive maintenance, slashing downtime by up to 45%. Green IT Panel’s guides decode tools like digital twins and neural networks for seamless adoption.
Solar ROI Surge
Manufacturers leveraging solar report 22% faster ROI post-2023 tax credits. Our portal breaks down hybrid systems, storage solutions, and grid independence strategies.
Zero-Defect Shift
Automated quality systems have reduced recalls by 60% in 3 years. Dive into sensor tech and real-time analytics driving the “perfect production” revolution.